Ice Cold Deliciousness
Blue Bell Creameries produces delicious ice cream in the quiet town of Brenham, Texas. HELUKABEL products endure a lot to help them do this.

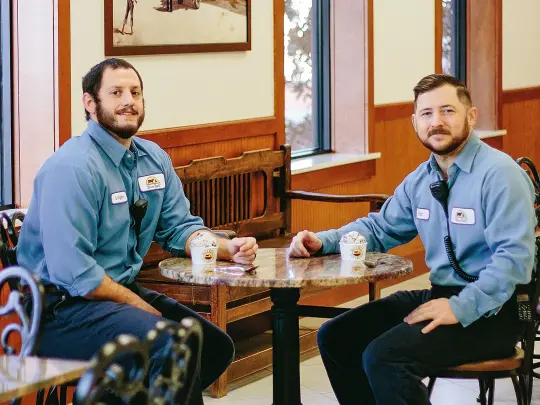
When the product developers at Blue Bell Creameries invented their Cookies ‘n Cream Ice Cream, they made a three-dimensional flavour. Logan Davis, engineering technician at the Blue Bell production plant, calls it a kind of “slow-exploding firework ”: first comes the rich and creamy, sweet vanilla; then the tongue finds the soft pieces of cookie – their crumbly sensation intensifies the taste. Finally, the main ingredient of the cookie pieces strikes – the dark, slightly bitter chocolate. It totally contrasts with them vanilla, which blends more and more into the background.
DEEP FREEZE FOR CABLES
Before the finished ice cream reaches the spoon and tongue, it travels a long way through Davis’ realm: from the large tanks where the milk, cream, vanilla, and chocolate cookies come together; into the machines that stir everything into fine, smooth ice cream; and finally to the container filling machine. Davis turns the tub in his hand and points out, “HELUKABEL products are used in each of these steps. We’ve been relying on them for seven years now. ” Why? “ Because cables often have a hard time surviving in our manufacturing environment and HELUKABEL’s quality is simply impressive.”
Everything must be meticulously cleaned in the production plant to ensure a safe, high-quality product is produced. “Blue Bell Creameries therefore insisted on cables with antibacterial properties and resistance to the detergents and other cleaners used during the washdown of the production plant,” says Neal Allen, vice president of engineering at HELUKABEL USA. This applies, for example, to the control cables for the mixing tanks as well as many other cables. “In addition, we use many drag-chain compatible types,” Davis adds. “We have heavily automated our manufacturing, so at the stations and between them, there are countless components in constant motion.”
And then of course, there are the cold rooms where the ice cream is cooled down to minus 40 degrees Celsius. Here, the cables have to cope with the strong vibrations from the freezer fans and extreme temperatures; conditions in which the cables previously used by Blue Bell Creameries failed. “They were a source of constant trouble,” says Davis. “The cold temperatures caused the cables to become brittle and then the vibrations made them crack.” He shakes his head and adds, “This exposed some of the copper!” This problem is one that he and his fellow engineering technician, Eric Gaskamp, could really do without. “Back then we had to change a cable every other week,” Gaskamp says. Davis sums up: “Since using HELUKABEL cables, we’ve never had any problems. What can I say, other than they have exactly the right cable for each of our applications.” “And the right accessories too,” adds Gaskamp. Therefore, Blue Bell Creameries also uses robust stainless steel cable glands among other accessories from HELUKABEL.
“It’s fun making something people enjoy,” says Davis. “After all, who doesn’t like ice cream? Since using HELUKABEL cables we’ve been able to do this without major incidents, which gives us more time to try our delicious ice cream.”
112 YEARS IN THE ICE CREAM BUSINESS
Who: Blue Bell Creameries; Brenham, Texas, USA; 3,650 employees
What: The family-owned company has been making ice cream since 1907. Today, so much ice cream rolls off the production line that 50,000 cows are needed to provide enough milk required for one day’s production. Sherbet and frozen snacks are also part of their product range. In addition to the main production site in Brenham, Blue Bell Creameries also has sites in Broken Arrow, Oklahoma and Sylacauga, Alabama.